Individual timber module construction
with DERIX
Modular construction with
a high degree of prefabrication
The advantages
of modular timber construction
- Cost and deadline certainty
The early planning depth enables a reliable project process.
- Short construction time with low emissions
The parallel construction of the foundation and prefabrication of the modules as well as the fast module assembly make a short construction time with low emissions possible.
- Solid construction
DERIX wooden modules are made of solid wood and are characterised by enormous robustness and stability.
- Quality
DERIX modules are manufactured under optimal industrial conditions with high precision and therefore achieve a consistently high quality.
- Sustainability
The use of wood as a natural building material with simultaneous substitution of concrete and steel leads to a significant reduction of the CO2 footprint. At the same time, wood is a natural, renewable raw material. Learn more about sustainable building with wood.
- Reduction of ancillary construction costs and site management
DERIX Module construction:
The project procedure
The foundation for a modular building is laid in the early design stage. Planning is carried out integrally on the digital twin of the building, so that all problems can already be solved in the model. Once this milestone has been reached, the modules are manufactured and, in parallel, the foundation work is carried out at the construction site. The assembly takes place with eight to ten modules per working day. The construction process at the building site is thus greatly shortened with the modular construction method and at the same time is characterised by low emissions and a smooth process. Feel free to contact us at the very beginning of your project.
Planning with
timber modules
A successful project is based on detailed, early planning. This applies in particular to the timber module construction method. Only a fully developed digital model is suitable as a basis for production. BIM (Building Information Modelling) has therefore been part of our daily work for a long time.
Our planning guide
1. Orthogonal axis –axis dimensions variable
2. Module sizes & room heights
3. Foundation/cellar conventional
Modular construction from
production to assembly
Technical specifications
for timber modules
Foundation
Foundation variants
Socket details
Construction
Building shell

Clinker facade
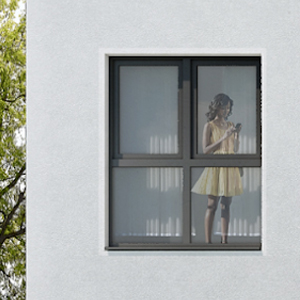
Plaster facade
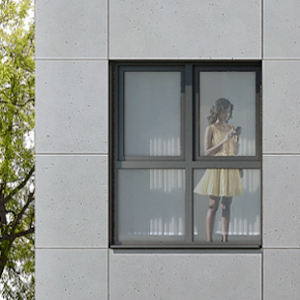
HPL facade
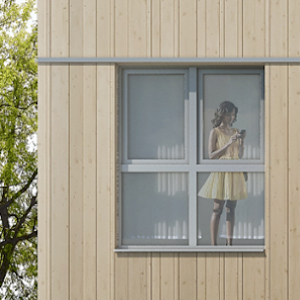
Wooden facade
Statics
The typology of small axis grids and double-shell components can be used effectively. At the same time, wood is very light, which favours the foundation.
Thin walls even in multi-storey buildings are common due to the predominantly linear load transfer. The same applies to the modular ceilings, which can be efficiently dimensioned. The same applies to the modular ceilings, which can be efficiently dimensioned. The flexible adjustment of component thicknesses makes it possible to think highly in terms of modular construction. The bracing of a modular building is carried out taking into account sound and fire protection requirements via the isolated design of a vertical module arrangement or by the design of effective ceiling panes per storey.
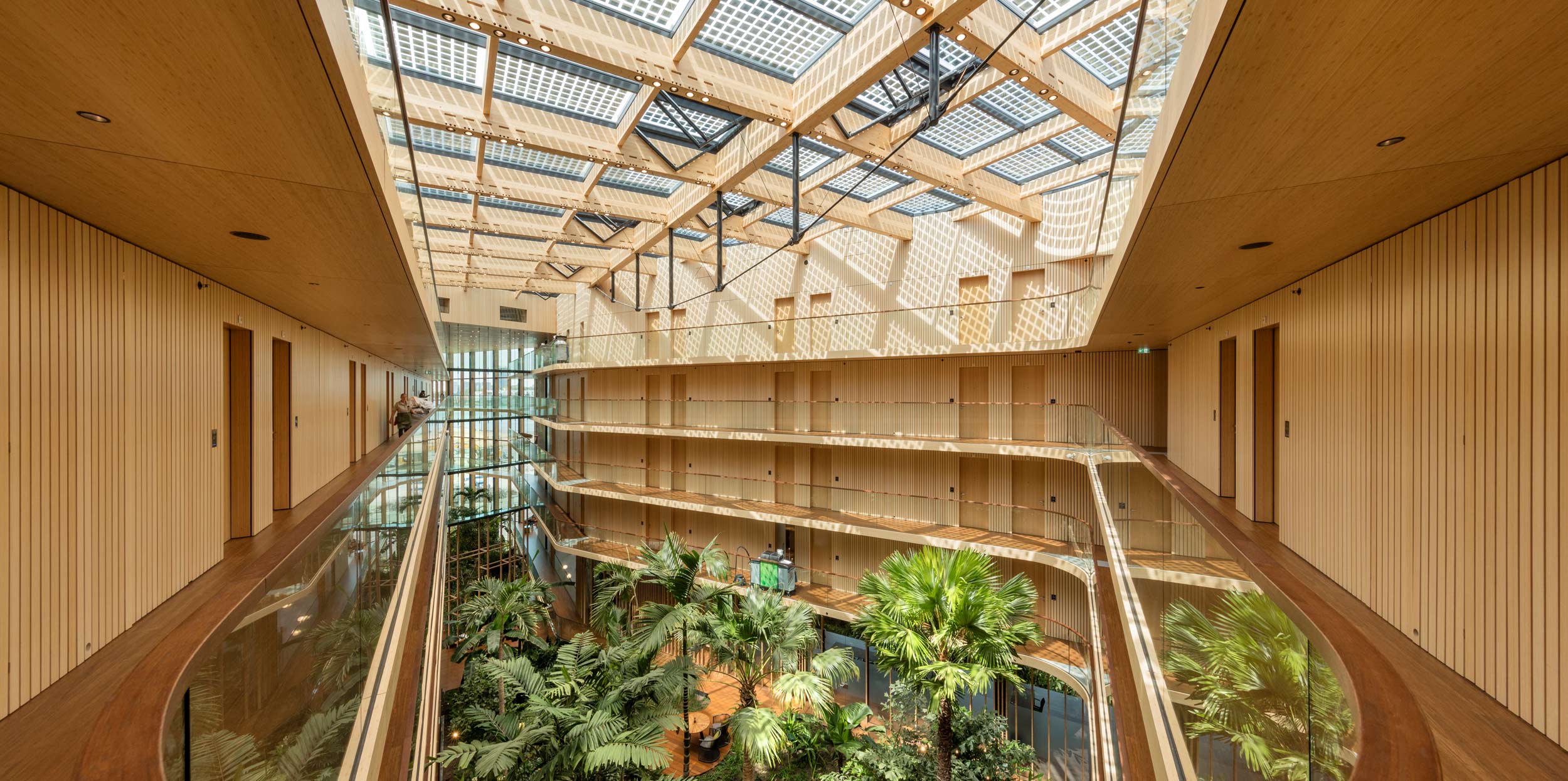
Fire protection
Wooden modular buildings meet the same protection targets and fire resistance durations as conventional buildings. In addition to taking the building regulations into account, the use of solid wood is also represented by the model timber construction guideline. Buildings up to building class 5 are possible under building law. The dimensioning of the components and the design of the module joints allow a flexible response to fire protection requirements.
Approved fire barriers are available for all media and resistance classes.
An examination of the respective state building code is necessary, as there are some differences between the states. Early dialogue with fire protection experts and building authorities ensures the feasibility of your project.
High level of protection in timber module construction
- Cavity-free construction thanks to solid wood and joint insulation
- Double protective effect due to double-shell design of the separating components
Sound insulation
Thermal insulation
BSE installations
The technical building equipment is already taken into account and fully modelled in the digital twin. Openings, socket and switch holes as well as cable routing are derived from this and created mechanically with CNC technology in X-LAM and glulam. Drill holes up to 1.35 m into the face of the X-LAM elements allow invisible cable routing even in exposed wood walls. The CNC machining of the components is carried out with the highest precision and completely replaces the classic carcass trades. The installation of the BSE components takes place in the factory. At the construction site, only the central building services and the supply lines are installed up to the transfer point at the module.